Products
Gravure Printing Ink Viscosity
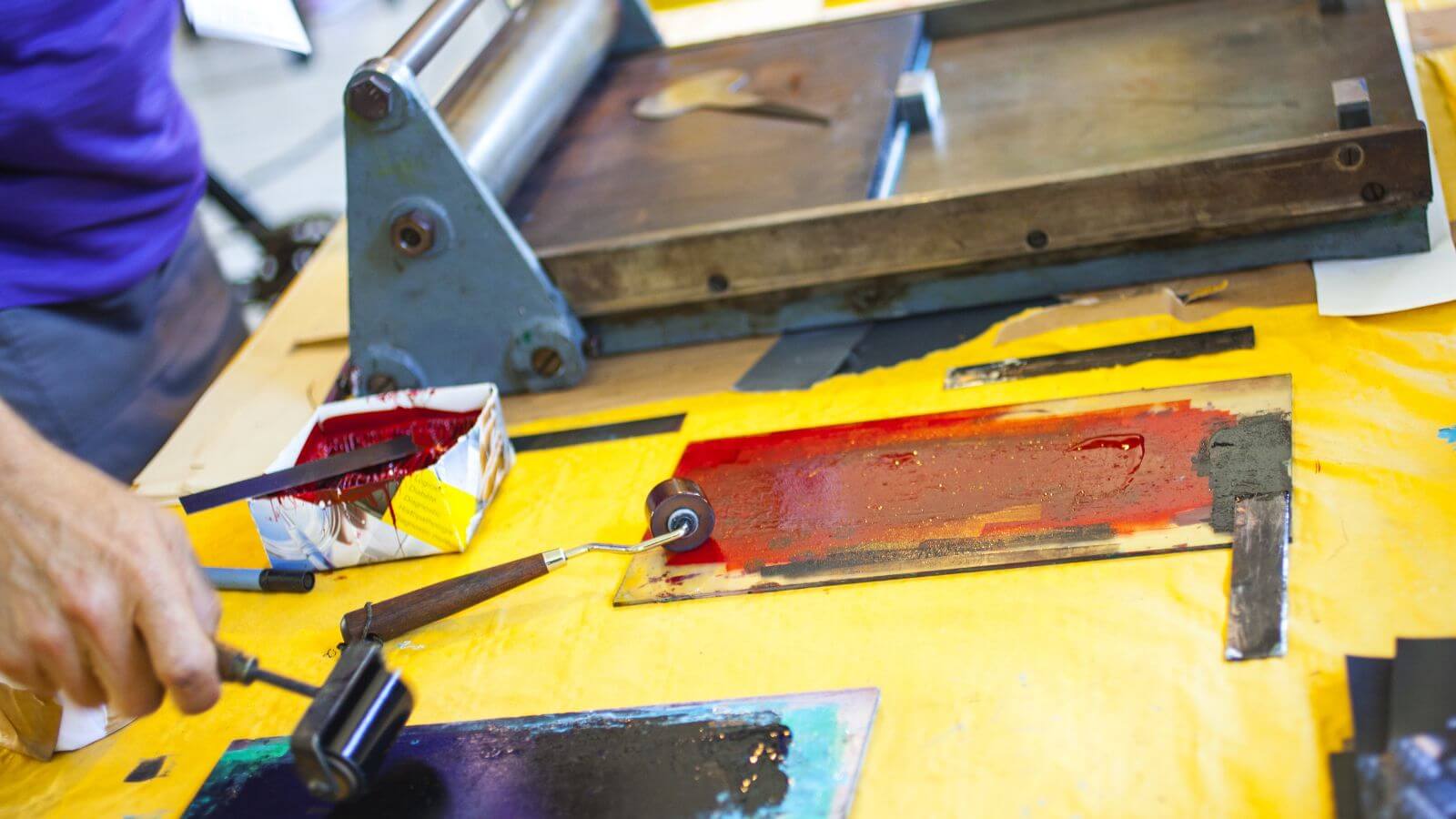
In order to improve the efficiency and printing effect of the rotogravure printing machine, we need to find the ideal point of ink viscosity. The following will introduce in detail how to find the ideal point of ink viscosity in high-speed rotogravure printing.
The ink is composed of organic solvents, binders, pigments, additives, auxiliary materials, etc. When these raw materials have been determined, the processing degree, method, and composition of each component have been determined, and the quality of pigment transfer is mainly related to the printing viscosity of the ink.
The practice has proved that the ink printing viscosity has a certain range (11~24S, use Zahn viscosity cup No. 3). The higher the ink printing viscosity, the worse the effect of pigment transfer. Because the role of the solvent is to dissolve resin or additives and auxiliary agents, etc., to give it fluidity so that the pigment is easily dispersed.
When the printing viscosity of the ink is too high, the entire ink system will be in an over-saturated state, and the pigments and other substances will have poor fluidity and cannot be dispersed uniformly, but form agglomerates and are easy to pile together so that the pigments cannot smoothly enter and exit the mesh. When the printing viscosity of the ink is too high, the pigment cannot even enter the mesh at all, let alone transfer. This is the so-called blocking phenomenon.
Therefore, we only need to make the colloidal system composed of resins, pigments, etc. and organic solvents not in an oversaturated state, but in a saturated or unsaturated state, so that the pigments and other substances can be well dispersed in it to form a uniform and delicate colloidal system. , So that the pigment enters and exits the mesh smoothly, and the problem can be solved.
Some ink manufacturers suggest that the printing viscosity of the ink is between 15~18S (Zahn viscosity cup No. 3). But in practice, especially in the high-speed gravure printing machine (printing speed is 100 ~ 260m/min), in order to ensure a good transfer effect, while printing for a long time, improve efficiency, the ink printing viscosity is generally 11 ~ 15S ( Zahn viscosity cup No. 3) to find its ideal state point.
In plastic gravure printing, the problem of dirty plates often occurs. The phenomenon is that the non-printing surface of the cylinder will also be stained with a hazy layer of resin (the resin is entrained with pigment) and transferred to the substrate, making the substrate appear flake or linear. The root cause of the dirty plate phenomenon is not only related to the hardness of the squeegee, the pressure of the squeegee, the contact angle of the squeegee, the quality of the plate cylinder, etc., but also the printing viscosity of the ink.
Contact Us Now
Enter your inquiry details, We will reply you in 24 hours.
Name can't be empty
E-mail can't be empty
Company can't be empty
Phone can't be empty
Phone
Products can't be empty
Products you want
Message can't be empty
Verification code error
Clear